Актуальность проблемы. Основой экономического и социального
развития СССР, достижения мирового научно-технического прогресса
является повышение производительности труда до 2000 г. в 2,3-2,5 раза.
Достигнуть таких высоких показателей в калийной промышленности
невозможно без широкого внедрения высокопроизводительной техники и
прогрессивной технологии добычи руды.
Применяемые в настоящее время на Верхнекамском месторождении технология очистной
выемки и комплексы горных машин характеризуются серьезными недостатками, основными
из которых являются низкая производительность труда и комбайновых комплексов,
высокие потери и разубоживание добываемой руды вследствие несоответствия
применяемой технологии и оборудования сложным горно-геологическим условиям,
рассогласованности параметров добычных и транспортных машин. В последние годы
наблюдается значительный рост технической производительности и энерговооруженности
горной техники. Осуществляется переход на комбайны «Урал-10А» и «Урал-20А» производительностью
5,0 и 6,0
т/мин. Прошли испытания и рекомендованы к серийному производству
самоходный вагон ВС-25Э и самоходный бункер-перегружатель БПС-22. Ведутся работы
по созданию комбайнов производительностью 10
т/мин и средств непрерывной
доставки руды из забоя. Поэтому при внедрении на месторождении таких высокопроизводительных
комплексов, актуальное значение приобретают вопросы разработки эффективной
технологии их применения, нахождения взаимно согласованных технических и
технологических решений, исследования и оптимизации основных параметров элементов подготовки и очистной выемки.
Цель диссертационной работы - разработать новую технологию
комбайновой выемки калийных пластов камерами в сложных
горно-геологических условиях Верхнекамского месторождения,
обеспечивающую улучшение основных технологических показателей добычи -
снижение потерь и разубоживания руды, повышение концентрации горных
работ, нагрузки на комбайновый комплекс и производительности труда.
Идея работы заключается в использовании особенностей залегания
калийных пластов на месторождении и процесса непрерывной отбойки и
доставки руды из забоя для оптимизации взаимосогласованных решений при
выборе рациональных параметров технологии.
Научная новизна.
1. Разработана имитационная модель
технологического процесса \2\ непрерывной добычи и транспортирования
руды из забоя, отличающаяся тем, что в ней отражены: неравномерность
комбайнового грузопотока за цикл отбойки серповидной заходки
исполнительным органом барабанного типа, длительность разворота
исполнительного органа комбайна для обратного хода и принцип реализации
грузопотока самоходным изгибающимся конвейером независимо от его типа и
конструкции.
2. Получены зависимости, определяющие рациональные параметры новой
технологии и устанавливающие взаимосвязь основных показателей
технологического процесса - производительности труда и комбайновых
комплексов с длиной камеры, мощностью пласта, вариантом выемки и
техническими параметрами оборудования, отличающиеся тем, что для
процесса непрерывной добычи и транспортирования руда из забоя они имеют
вид близкий к линейному по сравнению с выраженными степенными
аналогичными зависимостями для применяемой технологии.
3. Впервые установлены зависимости параболического вида, отражающие
изменение эффективности технологии выемки от состава комплексов и
технических характеристик оборудования, что позволило определить
область применения технологии с комплексами различного состава и
обосновать границу экономически целесообразного перехода от средств
цикличной доставки руды к непрерывной.
Достоверность научных положений, выводов и рекомендаций
обоснована: использованием в качестве исходной информации при
моделировании фактических значений параметров машин новых комбайновых
комплексов, полученных в результате их испытаний на месторождении,
адекватным воспроизведением на ЭВМ отличительных особенностей процесса
формирования и преобразования грузопотока комбайном с барабанным
исполнительным органом и самоходным изгибающимся конвейером,
удовлетворительной сходимостью теоретических и экспериментальных
исследований.
Практическая ценность работы заключается в разработке и
определении оптимальных параметров новой технологии с применением
высокопроизводительных комбайнов и средств непрерывной доставки руды
для рудников со сложными горно-геологическими условиями, в обосновании
рационального состава новых комбайновых комплексов и определении
области их эффективного применения. Реализация результатов исследований
позволит уменьшить разубоживание добываемой руды в 1,1-2,0 раза,
повысить производительность труда рабочих очистного \3\ забоя в 2,5?3,0
раза. Ожидаемый годовой экономический эффект составит 425,5 тыс.руб. на
участок.
Реализация работы. Материалы диссертационной работы были
использованы в «Расширенном технико-экономическом обосновании создания
комбайна «Темп-10», «Методических указаний по ведению горных работ на
Верхнекамском месторождении», «Пересмотре проекта отработки шахтного
поля рудника Четвертого калийного завода». По результатам исследований
разработаны «Исходные данные на проектирование опытно-промышленного
участка испытаний технологии выемки комбайном «Темп-10» с непрерывной
доставкой руды и гидрозакладкой выработанного пространства».
Апробация работы. Основные положения диссертационной работы
докладывались на отраслевых научно-технических конференциях молодых
ученых и специалистов (г.Солигорск, 1983 и 1986 гг.), на
научно-технической конференции Дома техники НТО по проблеме роботизации
и автоматизации производственных процессов (г.Пермь, 1986 г.), ежегодно
на научно-технических советах ВНИИГа и Уральского филиала ВНИИГа
(Пермь, Ленинград, 1983-1989 гг.), на III Всесоюзной конференции
молодых ученых (ИПКОН АН СССР, Москва, 1989 г.) и Всесоюзной
научно-технической конференции (МГИ, Москва, 1990 г.).
Публикация и объем работы. По теме диссертации опубликовано 7 печатных работ, получено 2 положительных решения ВНИИГПЭ.
Диссертационная работа состоит из введения, четырех глав и заключения,
изложенных на 140 страницах машинописного текста, содержит 41 рисунок,
30 таблиц, список литературы из 123 наименований и приложений.
Основное содержание работы
Особенностями Верхнекамского месторождения являются складчатость
калийных пластов как в широтном, так и меридиональном направлениях и
высокая вариация изменчивости их мощности. Кроме того непосредственная
кровля пластов в южной части месторождения неустойчива, склонна к
расслоению и обрушению и требует специальных мероприятий для
обеспечения безопасных условий труда. Применение комбайнов сплошного
резания типа «ПК» и «Урал» с фиксированным по высоте исполнительным
органом для отработки калийных пластов в таких горно-геологических
условиях приводит к технологическим потерям руды в камере, ухудшению
качества в результате прирезки пустых пород, потерям производительности
из-за несоответствия параметров \4\ исполнительного органа,
складчатости пластов и их мощности.
Принятая камерная система разработки характеризуется высокими потерями
полезного ископаемого в околоштрековых целиках, образованием, тем
самым, зон с повышенной концентрацией напряжений в массиве и снижением
производительности комплексов при зарубке.
Большой вклад в решение комплекса задач, связанных с повышением
эффективности комбайновой выемки калийных пластов на Верхнекамском
месторождении внесли ученые ВНИИГа, УралВНИИГа, БФ ВНИИГа, ЛГИ, ППИ,
ЛПИ, Гипроуглегормаша, Пермгипрогормаша, КарПТИ и других организаций.
Выполненные ими исследования были направлены на совершенствование
технологического процесса механизированной выемки, разработку
методических основ расчета и выбора оптимальных параметров техники и
технологии, создание перспективных средств добычи и транспорта руды.
На основе анализа этих работ и современного состояния комбайновой
выемки калийных руд в СССР и за рубежом были выделены прогрессивные
направления развития техники и технологии очистных работ, заключающиеся
в создании высокопроизводительных комплексов в составе универсальных (с
точки зрения возможности применения при различных системах разработки и
диапазона регулирования по вынимаемой мощности пластов) комбайнов и
средств непрерывной доставки руды из забоя. Одним из наиболее
эффективных методов для исследования новой технологии с применением
таких комплексов является метод имитационного моделирования.
С целью комплексного рассмотрения всего технологического процесса,
включающего технологию и механизацию очистной выемки, элементы
раскройки и подготовки шахтного поля рудника, оценку степени влияния
высокопроизводительного оборудования на экономические показатели добычи
и установление их оптимальных значений определены следующие задачи
исследований:
- выполнить анализ горно-геологических условий залегания калийных
пластов на месторождении, технологическую оценку нового горного
оборудования на основе теоретических исследований и результатов их
испытаний и обосновать рациональный тип и форму исполнительного органа
комбайна;
- разработать технологию очистной выемки с применением
высокопроизводительных комплексов для сложных горно-геологических
условий; \5\
- провести экспериментальные исследования на имитационных моделях и
установить влияние горно-геологических, технических и технологических
факторов на эксплуатационные показатели работы комбайновых комплексов;
- исследовать и обосновать оптимальные параметры технологических схем
выемки на основе экономико-математического моделирования элементов
технологии;
- выполнить оценку влияния высокопроизводительного оборудования на
календарное планирование ведения горных работ с учетом погодовой
стабилизации качества добываемой руды, технологическую схему раскройки,
подготовки и отработки шахтного поля и определить основные параметры
калийного рудника.
Сложные горно-геологические условия залегания калийных пластов на
месторождении выдвигают в число первоочередных проблем обеспечение
минимальных потерь и разубоживания руды, предъявляют повышенные
требования к диапазону и оперативности регулирования исполнительного
органа комбайна по мощности пласта.
Результаты проведенных на месторождении испытаний комбайнов «ПКЦ» и «
Heliminer»
с барабанным исполнительным органом показали, что они имеют ряд
принципиальных положительных отличий от комбайнов типа «ПК» и «Урал»,
основными из которых являются:
- возможность отработки калийных пластов переменной мощности за счет
плавного регулирования в определенных пределах высоты проходимой
выработки;
- снижение выхода в руде мелких (труднообогатимых) фракций;
- возможность улучшения качества отбитой руды за счет уменьшения
прирезки пустых пород из кровли пласта с высоким содержанием
нерастворимого остатка.
Исследование влияния формы и параметров исполнительных органов
комбайнов цикличного действия и типа «Урал» на технологические
показатели выемки (потери и разубоживание руды) показало, что наиболее
рациональным является барабанный исполнительный орган конусной формы.
Форма барабанного исполнительного органа оценивалась двумя параметрами
(рис. 1): углом конусности барабана

и коэффициентом формы барабана

.\6\
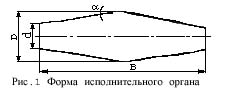
, (1)
(2)
где
D - диаметр барабана в центральной части,
м;
d - диаметр концевой части барабана,
м;
В - ширина исполнительного органа,
м.
Оптимальные технологические показатели выемки определены для различной
ширины исполнительного органа и интенсивности складчатости (табл. ).
Таблица
Оптимальные технологические показатели выемки при ширине исполнительного органа комбайна В=4,3 м
Интенсивность складчатости
|
Барабанный
|
Урал-10КС |
параметры
|
потери, n
|
разубоживание,

|
потери, n
|
разубоживание, 
|
Спокойная
|
= 1,8
|
0,037
|
0,008
|
0,084
|
0,011
|
=
5,3° |
Умеренная
|
= 2,0
|
0,063
|
0,106
|
0,106
|
0,021
|
= 6,0° |
Интенсивная
|
= 2,5
|
0,16
|
0,173
|
0,173
|
0,048
|
= 7,2° |
Технологические особенности комбайновой выемки на
месторождении, анализ изменения их основных параметров и результаты
испытаний комбайнов «ПКЦ» и «Heliminer» позволили считать данный тип
комбайнов рациональным и перспективным применением в калийной
промышленности комбайнов с упрощенным рабочим циклом. Поэтому в основу
\7\ вновь создаваемого институтом Гипроуглегормаш
высокопроизводительного комбайна «Темп-10» положены конструктивные и
технологические особенности комбайна «ПКЦ» с барабанным исполнительным
органом.
К основным технологическим и конструктивным элементам, определявшим
эффективную работу новых комбайновых комплексов отнесены: состав
комплексов, длина камеры, размеры панелей, блоков, полублоков,
одновременно находящихся в работе и их количество, объем
горно-подготовительных работ, расположение панельных блоковых выработок
и очистных камер.
Результаты испытаний и аналитические исследования процесса движения
самоходного изгибающегося конвейера на криволинейном участке камеры
позволили определить влияние радиуса кривизны участка зарубки, угла
расположения камер к оси выемочного штрека и скорости движения
конвейера и ленты на величину поперечной силы смещения конвейера.
Изменение угла проходки камер с 90° до 135° к оси выемочных штреков
позволило в 2 раза уменьшить действующие на конвейер поперечные
нагрузки на криволинейном участке камеры, тем самым повысить его
надежность и эффективность использования в комплексе.
В соответствии с этим и на основе составления матрицы возможных
сочетаний различных элементов технологии разработаны варианты
панельно-блоковой подготовки односторонних или двухсторонних (рис. 2)
блоков, наиболее полно отвечающие всем требованиям, предъявляемым к
новой технологии. Достоинства новых технологических схем заключаются в
том, что проходка камер под углом 135° к оси выемочных штреков
позволяет:
- сократить длину криволинейного участка в 2,5-3,0 раза и повысить
эффективность использования высокопроизводительных комбайнов «Темп-10»
на зарубке, надежность и эффективность работы изгибающегося конвейера в
комплексе;
- формировать систему с равножесткими целиками и уменьшить потери полезного ископаемого по камерному блоку на 3%.
Рис.2. Принципиальная технологическая схема панельно-блоковой
подготовки и очистной выемки с применением высокопроизводительных
комплексов
Для исследования и выбора рациональных параметров элементов технологии
была усовершенствована базовая система имитационного моделирования
«Синтранс. Версия II». Она дополнена новыми модулями, представляющими
работу комбайна с барабанным исполнительным Органом и самоходного
изгибающегося конвейера. Отличие работы нового комбайнового комплекса
заключается в изменении характера \8\ грузопотока и принципа
функционирования входящих в него машин. Работа комбайнов с барабанным
исполнительным органом представляется как последовательное выполнение
за время каждого полного цикла
tц.i четырех операций: зарубки
исполнительного органа в верхней части забоя
tз.i, отбойки с опусканием
исполнительного органа вниз
tотб.i, зачистки почвы выработки
tзач.i и
подъем исполнительного органа в холостую
tп.i.
Средний минутный грузопоток за цикл составит:
, т/мин. (3)
Фактический средний грузопоток может быть смоделирован, исходя из
представления, что за цикл отбойки руды комбайном, снимается
серповидная стружка, толщина которой равна глубине зарубки режущего
барабана. Поэтому средний минутный грузопоток определяется как:
, т/мин. (4)
, т/мин. (5)
, т/мин. (6)\9\
где:
Vц - объем руды, отбитой за цикл,
т;
В - ширина исполнительного органа,
м;

- объемный вес,
т/м3;
m - мощность вынимаемого слоя пласта,
м;
lз - глубина зарубки,
м;
Scmp - площадь вынимаемой стружки,
м2.
Результаты испытаний комбайнов «ПКЦ» и «Heliminer» показали, что
производительность при зарубке
Qз и отбойке
Qотб. различается по
величине и составляет
Qз = 0,6
Qотб.. Поэтому при моделировании
минутного комбайнового грузопотока дополнительно введен коэффициент
Km
, учитывающий эквивалентную производительность за цикл зарубки и
отбойки при различной мощности пласта.
Помимо особенностей формирования минутного грузопотока, отличие
комбайнов с барабанным исполнительным органом от комбайнов типа «ПК» и
«Урал» заключаются в отсутствии таких технологических стадий и
процессов как зарубка комбайна на камеру и отгон комплекса при
завершении проходки.
Математическое описание технологических процессов представлено как состояние работы и отказа функциональных элементов комплекса.
Состояние работы делится на следующее множество состояний:
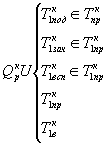
|
- выполнение подготовительных операций в начале смены
i = 0, 1, 2; |
- выполнение заключительных операций в конце смены
; i = 1,2,3; |
- вспомогательные операции, являющиеся функцией случайной величины
длины уходки Lух., распределенной нормально с параметрами mух, Gух; |
- состояние «Проходка»;
; |
- состояние «Вспомогательная стадия по развороту исполнительного органа комбайна для обратного хода»
m(Тв); (Tв). |
\10\
Аналогичная модель разработана для самоходного изгибающегося конвейера.
Особенностями взаимодействия комбайна и конвейера в новой технологии
является то, что сформированный комбайном грузопоток, независимо от его
величины, полностью реализуется самоходным изгибающимся конвейером.
Состояние работы конвейера характеризуется математическим ожиданием
наработки на отказ
(tр) и математическим ожиданием величины
(tв). Это значительно упростило математическое описание технологического процесса
выемки и расширило возможность по моделированию работы самоходного
изгибающегося конвейера, независимо от его типа и конструкции.
На основе постановки и реализации машинных имитационных экспериментов
для новой технологии получены близкие к линейным зависимости,
устанавливающие взаимосвязь горно-геологических, технических и
технологических факторов с эксплуатационными показателями работы
комплексов. Установлено, что увеличение мощности пласта с 3,0 до 6,0
м
приводит к повышению производительности в 1,25-1,3 раза.
Производительность комплексов на очистной выемке широкими камерами в
условиях устойчивых вмещающих пород снижается на 20-30% по сравнению с
вариантами отработки одноходовыми камерами.
При исследовании влияния параметров оборудования и состава комплекса на
технологические показатели добычи установлено, что для средств
цикличной доставки руды наибольший прирост производительности
обеспечивается при замене вагонов грузоподъемностью 15
т на вагоны
грузоподъемностью 25 и 35
т (рис.3).
Рис.3. Исследование производительности комплексов различного состава при базовой технологии:
----- комплексы с БП,
- - - комплексы без БП,
--.-- комплексы с резервным вагоном.
При минутной производительности
комбайна более 10
т/мин, применение самоходных вагонов любой
грузоподъемности не исключает простои комбайнов и не обеспечивает
полную реализацию технических возможностей комбайнов. Максимальный
прирост производительности комплекса за счет применения
бункера-перегружателя изменяется в пределах 35-45% и уменьшается с
увеличением минутной производительности комбайна и грузоподъемности
самоходного вагона. Производительность комбайновых комплексов,
включающих средства непрерывной доставки руды определяется, прежде
всего, минутной производительностью комбайна и количеством конвейеров в
комплексе (1, 2 или 3) (рис.4).
Рис.4. Исследование производительности комплексов при новой технологии:
----- комбайны S = 20 м2,
- - - комбайны S = 10 м2
Определена производительность труда рабочих очистного забоя при
различном составе комплекса и надежности оборудования. Наиболее
рациональным является комплекс с одним самоходным изгибающимся
конвейером, позволяющий при существующем уровне надежности оборудования
повысить производительность труда в 3,0 раза. \11\
Выбор оптимальных параметров элементов технологии осуществляется на
основе метода поэтапной оптимизации технологического процесса
комбайновой выемки. На первом этапе в качестве объекта принят добычной
горный участок, а критерия эффективности - удельные приведенные затраты
на добычу и транспортирование руды. Кроме этого, сравниваемые варианты
отличаются дополнительным показателем - качеством руды, добываемой
комбайнами с различной формой исполнительного органа. Оценку влияния
этого показателя производим по величине дополнительного эффекта или
ущерба от изменения качества руды в новом варианте:
, тыс.руб., (7) \12\
где
Ц - оптовая цена 1
т 95% KCl, руб./т;
С - себестоимость 1
т 95% KCI, руб./т;
Агод - годовая добыча руды, тыс.т;

- изменение выхода концентрата с 1
т руды, т.
Анализ затрат по подсистеме «Очистные работы» позволил определить
область эффективного применения технологии с комплексами различного
состава и обосновать границу экономически целесообразного перехода от
средств цикличной доставки руды к непрерывной (рис.5).
Рис.5. Область эффективного применения комплексов различного состава
I, II, III - количество конвейеров в комплексе ,
___.___ один резервный вагон на 2 комбайна.
При использовании средств цикличной доставки руды минимальные затраты
обеспечиваются перспективным комплексом с комбайном \13\
производительностью 7
т/мин., самоходным вагоном грузоподъемностью 35
т
и соответствующим ему по емкости самоходным бункером-перегружателем.
Применение одного забойного конвейера длиной 100
м с комбайнами,
имеющими площадь сечения выработок 20
м, становится эффективным при
производительности комбайнов более 8
т/мин. При проходке выработок
сечением 10
м2 применение конвейера в комплексе экономически
целесообразно уже при производительности комбайнов более 5
т/мин.
Анализ затрат, проведенный по подсистемам «Горно-подготовительные
работы» и «Транспорт» показал, что не зависимо от длины камеры,
наиболее рациональным является вариант полевой подготовки двухсторонних
блоков. Оптимальная ширина панели определяется нагрузкой на горный
участок и изменяется в пределах 1200-1400
м для рационального варианта
подготовки. Эффективность же новых вариантов в целом определяется,
прежде всего, составом комбайнового комплекса и соответствующей ему
длиной камеры. Наиболее рациональными являются варианты, где в состав
комплекса входит один конвейер длиной 200
м, что позволяет уменьшить
удельные приведенные затраты на 0,108-0,152
руб./т или на 12-15% по
сравнению с базовым вариантом. Ожидаемый экономический эффект от
внедрения технологии составит около 500 тыс.руб. на горный участок, из
них 45-55 тыс.руб. дополнительный экономический эффект от улучшения
качества руды, добываемой комбайном с барабанным исполнительным органом
конусной формы и рациональными параметрами.
Решая задачу разработки новой технологии выемки с
высокопроизводительным оборудованием, необходимо помимо оптимизации
параметров элементов технологии в отдельных подсистемах, определить их
влияние на качество функционирования всей технологической схемы
калийного предприятие, установить основные параметры рудника: схему
вскрытия, подготовки и отработки запасов шахтного поля, нагрузку на
участок и их количество в работе. Моделирование вариантов ведения
горных работ при базовой и новой технологии выемки с оптимальными
параметрами горного участка выполнено на ЭВМ. В качестве критерия
эффективности сравниваемых вариантов принята величина относительного
экономического эффекта за весь период отработки запасов шахтного поля.
, тыс.руб., (8 ) \14\
где
Si - стоимость товарной продукции (концентрата) за срок отработки по i-тому варианту;
3i - приведенные затраты на выпуск товарной продукции за срок отработки запасов по i -тому варианту;
Пi - предстоящие затраты на компенсацию срока службы предприятия.
В результате исследований применения новой технологии выемки на примере
шахтного поля БКЗ-4 установлены оптимальные параметры рудника.
Технологическая схема предусматривает сохранение панельно-блоковой
подготовки с комбинированным порядком отработки шахтного поля. Для
проектирования новой технологии рекомендуются следующие исходные
данные: среднегодовая мощность рудника = 13,5 млн.т/год, нагрузка на
участок = 2,7 млн.т/год, количество одновременно отрабатываемых панелей
- 5, количество комбайновых комплексов в панели - 7 комп., в том числе
на пласте Кр.II - 2 комплекса с комбайном «Темп-10», на пласте «АБ» и
подготовке 5 комплексов с комбайнами «Урал-10КС» или «ПКЦ». Ширина
панелей 1200
м, длина - 3000
м. Расположение блоков под углом 45° к оси
панельных выработок, блоки двухсторонние (односторонние), ширина блока
400
м (200
м). \15\
ЗАКЛЮЧЕНИЕ
В диссертационной работе дано решение актуальной задачи повышения
эффективности отработки калийных пластов в сложных горно-геологических
условиях, состоящее в разработке технологии выемки с применением
высокопроизводительных комплексов, обосновании рациональных параметров
элементов технологии, определение степени их согласованности и влияния
на технологические показатели добычи.
Основные научные результаты, практические выводы и рекомендации заключаются в следующем:
Разработана новая технология непрерывной добычи и транспортирования
руды из забоя, позволившая за счет рационального расположения очистных
камер к блоковым и панельным штрекам, поиска оптимальных технических и
технологических решений повысить эффективность использования
высокопроизводительных комплексов на очистной выемке, увеличить
извлечение полезного ископаемого по камерному блоку на 3% и уменьшить
разубоживание добываемой руды в 1,1-2,0 раза.
Разработана имитационная модель технологического процесса комбайновой
выемки и выполнено математическое описание новых модулей, позволивших,
в отличие от применяемой технологии, описать неравномерность
комбайнового грузопотока за цикл отбойки руды, изменение операций в
технологическом цикле и принцип преобразования грузопотока самоходным
изгибающимся конвейером не зависимо от его типа и конструкции.
На основе постановки и реализации машинных имитационных экспериментов
для новой технологии установлены близкие к линейным зависимости
основных показателей процесса выемки - производительности труда и
комбайновых комплексов от длины камеры, мощности пласта, варианта
выемки и технологических параметров оборудования. Наиболее рациональным
является вариант отработки калийных пластов одиночными камерами
комплексом в составе комбайна «Темп-10» и одного самоходного
изгибающегося конвейера, позволяющий повысить производительность труда
рабочих очистного забоя в 2,5-3,0 раза.
Разработана экономико-математическая модель «Горный участок»
включающая, помимо основного критерия «удельные приведенные затраты»,
дополнительный показатель - извлечение полезного компонента на фабрике,
в зависимости от качества руды, добываемой \16\ комбайнами с различный
типом и формой исполнительного органа, что позволило определить
рациональные параметры новой технологии и установить оптимальные
технологические показатели выемки по условию потерь и разубоживанию
добываемой руды.
На основе исследования экономико-математической модели установлены
зависимости параболического вида, отражающие изменение эффективности
технологии выемки от состава комплексов и технических характеристик
оборудования, позволившие впервые определить область применения
комплексов различного состава. Установлено, что переход на непрерывную
доставку руды в калийной промышленности экономически целесообразен на
проходке выработок сечением
S = 20
м2 при производительности комбайна
более 8 т/мин., а на проходке выработок сечением
S = 10
м2 при
производительности комбайна более 5
т/мин.
Наиболее рациональным является вариант панельно-блокового способа
полевой подготовки двухсторонних блоков с прямым или обратный порядками
отработки панелей и обратным порядком отработки блоков. Оптимальная
ширина панели равна 1200-1400
м.
Разработаны рекомендации для проектирования новой технологии выемки
высокопроизводительными комплексами применительно к условиям рудника
БКЗ-4. Технологическая схема предусматривает сохранение принятой на
руднике раскройки шахтного поля с комбинированным порядком отработки
запасов. Рекомендуется принять следующие оптимальные параметры:
среднегодовая мощность - 13,5 млн.т/год, нагрузка на участок - 2,7
млн.т/год, количество одновременно отрабатываемых панелей - 5 и
количество комбайновых комплексов на панели - 7. Реализация
рекомендаций обеспечивает стабилизацию качества добываемой руды,
повышение по сравнению с базовым вариантом, концентрации объемов
производства на 10% и концентрации горных работ на 45%.
Результаты исследований были использованы при разработке «Исходных
данных на проектирование опытно-промышленного участка испытаний
технологии», «Пересмотре проекта отработки шахтного поля рудника ЕКЗ-4»
и в «Методических указаниях по ведению горных работ на Верхнекамском
месторождении». Ожидаемый экономический эффект составит 425,5 тыс.руб.
в год на участок.
Основные положения диссертации опубликованы в следующих работах: \17\
1. Исследование возможности повышения использования комбайновых
комплексов на рудниках ПО «Сильвинит». /Леонович М.Ф., Ковтун В.Я.,
Мухин И.Д., Воробьев В.А. / Горний журнал, 1984, № 12, с. 31-33.
2.
Воробьев В.А., Ковтун В.Я., Рогальников В.И.
Форма и параметры исполнительного органа комбайна для разработки
калийных пластов // Повышение извлечения и качества руды при разработке
калийных месторождений: Сб.науч.тр. /ВНИИГ. - Л., 1985г., с. 26-30.
3.
Воробьев В.А., Леонович М.Ф., Чертищев О.В.
Исследование влияния параметров надежности на производительность
комбайнового комплекса методом имитационного моделирования на ЭВМ
//Тез.докл. научно-практической конференция молодых ученых и
специалистов «Роботизация и автоматизация производственных процессов».
- Пермь, 1986, с. 37.
4.
Березин Е.П., Леонович М.Ф., Воробьев В.А.
Оценка влияния уровня надежности горных машин на производительность
комбайнового комплекса //Системы транспорта горнорудных предприятий:
Сб.науч.тр. /КарПГИ. - Караганда, 1987, с. 19-24.
5.
Леонович М.Ф., Воробьев В.А., Пинский В.Л.
Выбор рациональных параметров и оценка области эффективного применения
комбайновых комплексов со средствами цикличной и непрерывной доставки
руды в камерах //Совершенствование добычи калийных руд в сложных
горно-геологических условиях: Сб.науч.тр. /ВНИИГ. - Л., 1988, с. 17-23.
6.
Воробьев В.А., Леонович М.Ф.
Методические особенности расчета эксплуатационной производительности
комплексов с комбайнами избирательного действия на подземной добыче
калийной и каменной соли /Урал. филиал ВНИИГ. - Пермь, 1989, с. 10. -
Деп. в отд.НИИГЭХИМ (г.Черкассы) 07.06.89, № 520 ХII-89.
7. Состояние и основные направления развития техники и технологии
добычи калийных руд Верхнекамского месторождения /Соловьев В.А., Бей
М.М., Вилесов В. В., Воробьев В.А. /Тез. докл. Всесоюзной
научно-технической конференции в МГИ. /Теория и практика
проектирования, строительства и эксплуатации высокопроизводительных
рудников. - M., 1990, с. 65.